Automated End-of-Line Surface Inspection For Forged Rim Manufacturer
Implementing an automated inspection system using synthetic data to enhance the accuracy and efficiency of surface inspections for forged rims.
Problem
In the automotive industry, the forging process is widely used to manufacture high-performance components like rims due to its ability to create strong, lightweight parts. However, ensuring the highest quality of forged rims is crucial for both customer satisfaction and safety. Even minor defects, such as dents or scratches, can affect the rim's structural integrity and aesthetic appeal, making accurate and reliable surface inspection essential.
Forged rims often feature complex geometries, making it challenging to detect minor surface defects. The subtle differences in size and shape between numerous product variants further complicate the inspection process. Adding to the complexity, these rims arrive for inspection in random sequences, requiring a versatile system to handle various products efficiently.
Manual visual inspections, which remain common in the industry, suffer from slow productivity and inconsistent quality due to human subjectivity and fatigue. These manual methods not only reduce inspection efficiency but also result in varying defect detection rates. Given the critical nature of automotive parts, customers are particularly sensitive to even the smallest defects, driven by both aesthetic and safety concerns.
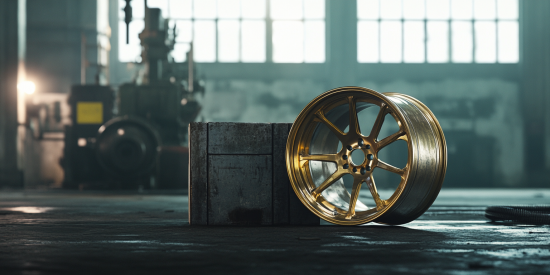
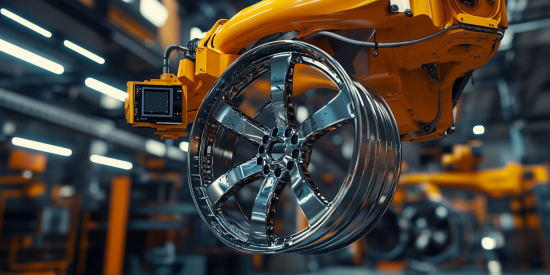
Goal
The primary goal is to enhance the accuracy and consistency of quality inspections by implementing automated solutions that reduce reliance on manual efforts. By doing so, we aim to significantly increase productivity and reduce cycle times, enabling faster and more efficient operations. Additionally, the system will be designed with the flexibility to adapt seamlessly to new product variants, ensuring scalability and long-term viability for evolving manufacturing needs.
Solution
The solution involves partnering with a robotics company to create an automated inspection line, eliminating the need for manual inspection and boosting efficiency. By leveraging synthetic data, we can rapidly develop and deploy robust inspection algorithms. These algorithms are embedded into a versatile application that first identifies the object to be inspected, then performs the appropriate inspection based on the product variant or type. This ensures adaptability across different product lines.
The inspection system is designed to handle even rare defects and can operate effectively under varying lighting conditions, providing consistent, high-quality results. Additionally, the system stores and analyzes inspection data, allowing continuous optimization of the application over time. This also enables the integration of predictive maintenance, further improving operational efficiency and reducing downtime.
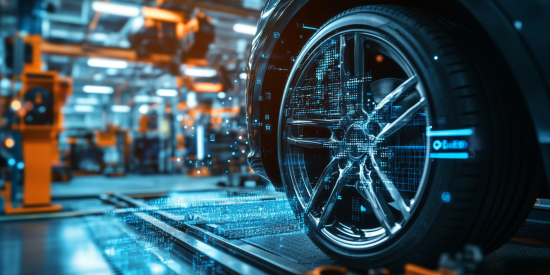
Customer Value
By replacing manual visual inspections with an automated system driven by synthetic data, the rim manufacturer can now ensure objective, consistent quality assurance while enhancing overall product quality. The system’s ability to reduce cycle times, combined with time and cost savings when adapting to new product variants, significantly boosts productivity. Additionally, the storage and analysis of inspection data enable predictive maintenance and ongoing process improvements, optimizing the entire production system over time.