Reducing Pseudo Rejects Through Spatially-Resolved Defect Analysis
By using pose estimation and a 3D-2D-mapping approach, it is possible to go much beyond simple anomaly detection in order to improve quality assurance for high-volume production.
Problem
Injection molding is widely used to manufacture plastic parts for multiple industries due to its ability to produce high volumes at low cost. However, in high-volume production environments, low cycle times and reliance on simple anomaly detection lead to a high rate of false positives, resulting in costly pseudo rejects that could otherwise be avoided.
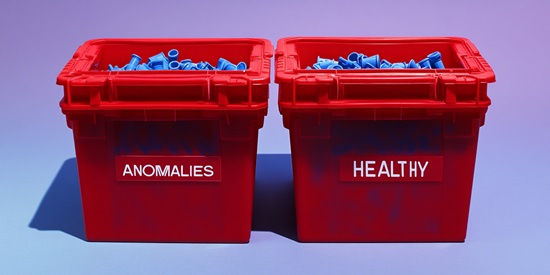
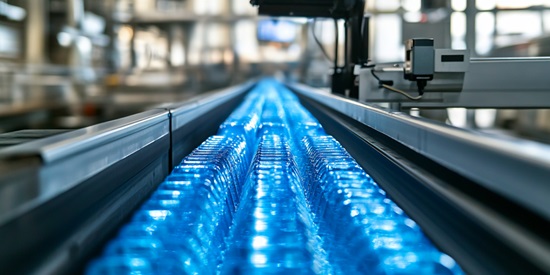
Goal
The goal is to improve inspection quality and significantly reduce pseudo rejects while maintaining the use of existing hardware and ensuring low cycle times.
Solution
The solution replaces basic anomaly detection with a detailed defect classification system, enabling spatially-resolved defect analysis through pose estimation and a 3D-2D-mapping approach. This allows the system to distinguish critical defects in key areas of a product from non-critical defects in less important regions. Leveraging synthetic data generation, the system is rapidly developed and is robust enough to handle even rare defects.
The solution integrates seamlessly with existing hardware, using standard communication interfaces, and provides rapid local deployment to maintain low cycle times. Additionally, the inspection results are stored for continuous system improvements over time.
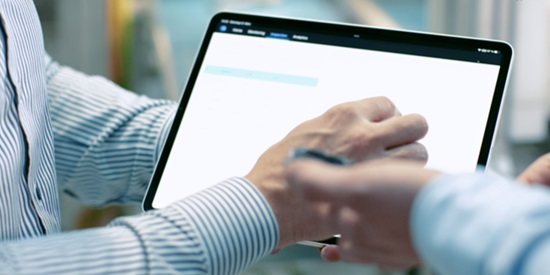
Customer Value
Through the combination of synthetic data generation and spatially-resolved defect analysis, the customer gains the ability to conduct much more detailed and tailored inspections. Defects like scratches or dents can now be evaluated based on their location on the product, allowing the customer to distinguish between critical and non-critical areas. This advanced inspection capability not only reduces pseudo rejects but also optimizes overall product quality without compromising on production speed.